As the absolute reliability of the cooling system is essential for our customers we have collected in this article some key principles which should definitely be considered when selecting the cooling system.
In following chapters we tell about the importance of certified components, expansion tank technology including leakage detection functions and also about the material and coolant selection.
Robust and certified products
Especially at marine sector it is important to use only marine approved components. This requirement is also stated by several classification societies.
The design in Adwatec products is very robust and made for tough marine conditions. Our commitment to quality is reflected in the DNV type approval we have received for our standard C-series products. Additionally, we have subjected our cooling station type CCE153R to a vibration test at Eurofins laboratory in accordance with DNV rules.
Adwatec C-series design utilizes a manifold construction which significantly minimizes the number of components required, resulting in fewer connection points, and therefore reducing the likelihood of leaks.
In our standard cooling stations we use components that have a minimum IP54 rating while materials in steel structures are selected according to required corrosion classification grade of a standard EN 12944.
Closed-type cooling circuit provides many benefits
Circulation systems can be classified into two types: open systems and closed systems. An open system isn’t pressurized and allows free contact with air, while in a closed system the piping is completely air-tight and the pipelines are pressurized.
At Adwatec, we specialize in delivering only closed-type cooling systems as they are the most efficient way to prevent oxygen diffusion in the coolant and to reduce the risk of electrochemical corrosion.
Closed-type cooling stations enables also other significant benefits. With our advanced technology of closed-type expansion tanks we can provide you
- an accurate leakage detection system based on the tank coolant level measurements
- a visual coolant level indicator and
- an extremely fast de-airing system (Adwatec 60min vs. others 12 hours
Additionally, there are no need for spare part tanks as we don’t use a short-lifecycle bladder or membranes in our tanks.
Properly chosen piping materials
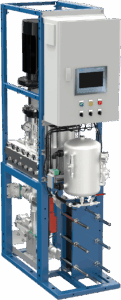
To eliminate the risk of a galvanic corrosion it is essential to use only compatible materials in water cooling circuits.
We have earlier published an excellent article about the Material selection in water cooling systems. In this article we tell how to select piping materials to ensure long lifecycle of the cooling system.
At Adwatec we want to keep it simple and we are using only high-quality stainless steel and aluminium parts in piping components. Aluminium parts will be coated if customer has copper parts in their cooling circuit.
When it comes to material selection of the plate heat exchanger this is always made according to project specific needs.
- If process water is available, the plates used in our heat exchangers will be made from stainless steel. The bonding method of the plates can be accomplished using all-stainless, copper brazing, or rubber gasketing, depending on the type of power electronics involved. The selection of the attaching method will be carefully chosen to ensure optimal performance.
- If sea water is available, the plates used in our heat exchangers will be made from titanium to ensure corrosion resistance and durability. (see picture 1:
ACE154R)
To minimize the risk of corrosion, we highly advise against using copper, brass, or carbon steel materials in the power electronics cooling circuit. If the use of these materials cannot be avoided, please inform us beforehand so that we can prepare the cooling station accordingly.
Importancy of the coolant selection
Properly chosen coolant is the most efficient way to ensure long lifecycle of the power electronics and cooling station.
While ethylene glycol and propylene glycol can be used as coolants, they alone do not have especially good corrosion resistance properties. Therefore, it is necessary to add a corrosion inhibitor such as Cortec VpCI-649 to the coolant. Some heat transfer fluids, such as Clariant Antifrogen N (monoethylene glycol) or Antifrogen L (monopropylene glycol), already contain inhibitors. When selecting the correct coolant, compatibility with aluminum must be
confirmed.
Adwatec recommends using a glycol-based coolant with a concentration between 20-30%, as this ratio offers adequate corrosion resistance while minimizing the reduction of cooling capacity caused by glycol. The manufacturer’s recommendation must be checked to ensure that the glycol concentration is sufficient for full corrosion protection.
If an outdoor-installed water-to-air heat exchanger is part of the cooling circuit, the glycol concentration will be chosen according to the ambient outdoor temperature.
If the power electronics require deionized, low-conductivity coolant, the appropriate choice is a water-propylene glycol mixture without inhibitors, as the deionizing system would remove inhibitors from the coolant, potentially lowering the deionizer’s lifetime.
Teemu Alajoki
Technical Manager, MSc