In power electronics, a liquid cooling system is always an essential slave system for some major functions like AC propulsion drive of a ship or AC/DC station of a HVDC link connected to a national grid as examples. A failure of cooling is an immediate risk for the master operation and may result in huge consequences in many applications. This is, why quality and reliability are so important for power electronics’ cooling systems.
The cooling media – the coolant – is like the blood in the human body serving several vital functions. The coolant is a key factor for reliability at the start-up and during the long-term operation. The start-up procedures impact the long-term quality, which is built-up with several practical design features and good workmanship, such as:
- Pipelines and cooling system are clean from manufacturing impurities
- Pure coolant is kept clean and filled easily into a loop
- There is an arrangement for a fast air bleeding from the system to prevent cavitation and minimize free oxygen inside the cooling loop
- Condition of the coolant is observed and recorded
- Tightness of the complete system is tested and guaranteed for a long operational time
A major operational challenge for a liquid cooling system is to keep the coolant flowing and in a good condition. The functioning of the process and components is partly a result of the healthy coolant. The selection of the best coolant for an application and the correct components and materials for the process ensure the reliable operation for the cooling and for the important master system. The communication from the cooling to the master system prevents vain trips and interruptions.
Typical coolant alternatives
Materials for the cooling process components
Optimal, but not always possible, case would be that all metal parts in contact with coolant would be of austenitic stainless steel. In very critical applications like pharmaceutical water loops, this is a typical requirement. Type AISI 304 and 316 (EN 1.4301 and 1.4401) are widely used in the cooling systems and there is no practical difference between these alloys. Much bigger issue are possible manufacturing impurities and poor pickling of weld seams. AISI 304, even being less alloyed with chromium and nickel, has shown better behaviour in systems with higher alkalinity water.
In many cases where component availability and other design issues create limitations the cooling systems typically include also other wet materials than stainless steel. Then connecting components and materials to each other should be considered carefully. The possibility of formation of galvanic pairs and corrosion should be paid attention to. Coolant will be an electrolyte, weaker or stronger, and various materials can create galvanic pairs
Picture 1 shows four simplified cases to connect various materials to each other in a cooling loop. Two upper cases have no risk of the galvanic corrosion. There is a non-conductive sealing but no “wet” connection between the metals A and B. Instead, two lower cases have the risk for the galvanic corrosion.

Electrochemical voltages of typical materials used in the cooling loops are shown in Picture 2. The galvanic corrosion will occur when cathodic and anodic metals are in contact in and around the water systems. The potential for different metals to be an anode versus a cathode is shown in this picture. The larger the difference between two materials in the electrochemical voltage, the larger the potential for the galvanic corrosion.
These charts are often presented with the seawater as the electrolyte. This is naturally not the situation for the primary cooling loops of the power electronics. In the marine applications, the secondary loop can be done with seawater
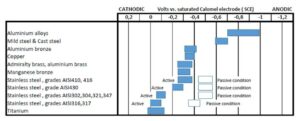
The typical coolant alternatives explained above are much weaker electrolytes than the sea water but relative activity of various materials is about the same. The tap water is the “strongest” electrolyte even thou sodium chloride content is low. De-ionized water, having very low conductivity, does not create electrolyte at all. But on the other hand, de-ionized water is in very unstable condition and tries to get ions out of even stainless steel to get back to “normal” and “pollutes” itself. A phenomena called “rouging” is sometimes found in high purity hot water loops, where only stainless steel is used. It appears as thin red or black deposit in the pipes and surfaces.
Cu-based metals cannot be used with de-ionized water. De-ionized water will rip Cu ions from any copper in the system, contaminating the water and corroding all copper in the system.
De-ionized water with glycol is the “worst” electrolyte out of described alternatives and with low oxygen content the risk for galvanic corrosion is minimized. The closed cooling loop with over pressure and effective bleeding system creates a good base for a reliable operation.
Learn more about Adwatec water cooling solutions
WORDS: Jorma Terävä, MSc in Eng. Senior Advisor, Adwatec Oy.
For more information please contact Ismo Lehtonen, Sales and Marketing Director
+358 40 669 2220
ismo.lehtonen@adwatec.com