Article about coolants published in Electric & Hybrid Marine Technology International Magazine April 2024 issue. Click the image for magazine version.
Specifying cooling systems
Water is an excellent medium to remove heat from heat loads like power electronics or batteries. Too often water or liquid cooling is, however, claimed to be unreliable or complicated. That doesn’t need to be the case when certain basic matters have been properly considered during the product engineering, manufacturing, and commissioning and everyday use. The focus here is the coolant!
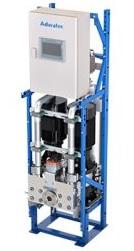
What coolant to use?
The coolant to be used will be specified by the power electronics equipment supplier. Ethylene glycol and propylene glycol can be used as coolants. However, they alone do not have especially good corrosion resistance properties. Therefore, it is necessary to add a corrosion inhibitor to the coolant. Some heat transfer fluids already contain inhibitors.
Typically, a glycol-based coolant with a concentration between 20-30% offers adequate corrosion resistance while minimizing the reduction of cooling capacity caused by glycol.
If an outdoor-installed water-to-air heat exchanger is part of the cooling circuit, the glycol concentration will be chosen according to the ambient outdoor temperature.
How to avoid galvanic corrosion?
All metals have a galvanic potential. When there is a connection between two metals that have a different galvanic potential, a galvanic circuit is formed and galvanic corrosion may find place. The cooling liquid acts as a “connector” between the metals. Galvanic corrosion can be minimized by using non-conductive materials between metals (i.e. plastic or rubber) and thus disconnecting the galvanic circuit. The recommendation is to use stainless steel and high-grade aluminum (6000-series) and avoid copper and carbon steel-based materials. If, however, copper materials are used, then aluminum shall not be used.
There are two types of cooling circuits: open systems and closed systems. An open system isn’t pressurized and allows free contact with air, while in a closed system the piping is completely airtight and the pipelines are pressurized. Closed-type cooling systems are the most efficient way to prevent oxygen diffusion in the coolant and to reduce the risk of electrochemical corrosion

Particles in the circuit?
During the manufacturing and installation process anything can and will happen. Thus, also metal and other particles may end up in the power electronics piping, cold plates and cooling system. It is a must to ensure that the system is clean. This can be done by flushing the system. Also later, during the operation when following the maintenance instructions and renewing the coolant, the system flushing is important to remove particles that may have appeared in the system.
Small particles cause wear and tear in the cooling system components and may lead to galvanic corrosion. They may block tiny cooling channels in cooling elements leading to heat problems as well.
Some cooling units have an inspection window through which the quality of the coolant can be checked.
The cooling unit storaging
Often the equipment will not be installed and comissioned immediatelly after manufacturing but storaged for later use. Wrong coolant inside the cooling unit or no coolant at all may cause severe damage. Here it is important to ensure that the equipment is storaged following the manufacturers instructions.
Words:
Heikki Mustonen
Managing Director